Manufacturing Processes of Apalutamide API
Apalutamide API is a non-steroidal antagonist of the androgen receptor, employed for treating prostate cancer. It functions by inhibiting the androgen receptor, thereby hindering the growth and proliferation of cancerous cells. This inhibition ultimately improves patient survival rates and quality of life. Apalutamide’s chemical structure incorporates multiple fluorine and nitrogen atoms, granting it specific physicochemical and pharmacological properties.
Beyond its function in prostate cancer therapy, Apalutamide API holds promise for the treatment of other malignancies that are sensitive to androgens. Ongoing research is exploring its potential applications in this regard.
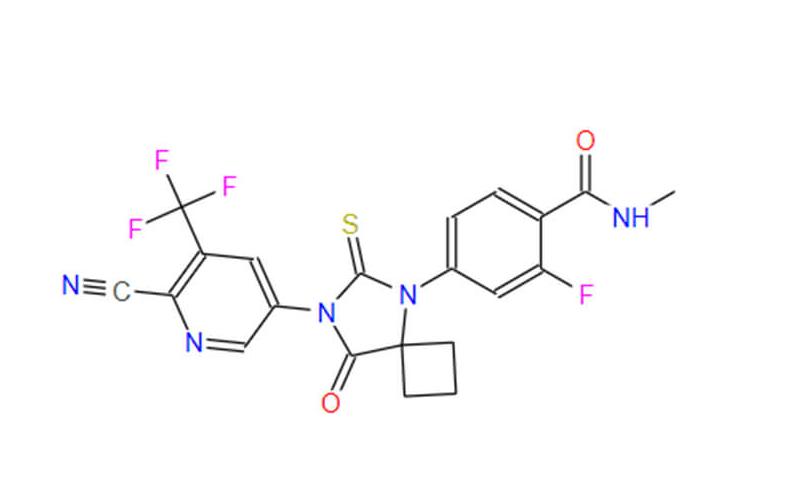
Supply Chain of Apalutamide API
The global market for Apalutamide API is populated by numerous pharmaceutical companies engaged in its production and distribution. When selecting a manufactuer, various factors come into play:
- Reputation and Track Record: Opting for a reputable Apalutamide manufactuer with a proven track record of quality and reliability is pivotal.
- Manufacturing Capabilities: Assessing the supplier’s manufacturing facilities and their adherence to GMP regulations is crucial.
- Regulatory Compliance: Ensuring the supplier operates in compliance with relevant regulatory requirements is essential.
- Cost-Effectiveness: While cost is a consideration, it should not compromise quality. Striking a balance between cost and quality is necessary.
Manufacturing Processes and Quality Control of Apalutamide API
The production process of apalutamide API is a multi-stage choreography, meticulously crafted to ensure efficiency and high-quality output. Here’s a deeper dive into each of the key steps:
1. Reaction Steps:
This stage forms the heart of the production process, where the actual chemical transformations occur according to the designed synthetic route. Each reaction involves specific starting materials and requires precise control of various parameters.
- Mixing: Precise amounts of starting materials, solvents, and catalysts are carefully mixed to initiate the desired reaction. Uniform mixing ensures all components are readily available for reaction, maximizing efficiency.
- Reaction Conditions: Factors like temperature, pressure, pH, and reaction time are meticulously controlled. Deviations from these parameters can lead to undesired side reactions, reduced yield, or product degradation.
- Monitoring and Control: The reaction progress is continuously monitored, often through real-time analytical techniques. Adjustments to reaction conditions may be made to ensure the reaction proceeds as planned.
- Quenching: Once the reaction reaches completion, it’s quenched by introducing a specific reagent to stop the reaction and prevent further product degradation.
2. Intermediate Purification:
After each reaction step, the desired intermediate product needs to be isolated and purified from the reaction mixture. This step is crucial for ensuring the success of subsequent reactions. Common purification techniques employed include:
- Crystallization: The desired intermediate is selectively crystallized from the reaction mixture by manipulating factors like temperature and solvent composition. This technique takes advantage of the differing solubility of the target molecule compared to impurities.
- Chromatography: This technique utilizes a stationary phase (solid or liquid) and a mobile phase (liquid or gas) to separate components based on their size, polarity, or other chemical properties. Different chromatographic techniques like column chromatography or preparative HPLC can be used depending on the specific intermediate.
- Filtration: Solid impurities or catalyst residues can be removed through filtration techniques like vacuum filtration or centrifugation.
- Washing: Washing with appropriate solvents helps remove residual impurities that may not be effectively separated by other purification methods.
3. Product Extraction and Purification:
After the final reaction step, the focus shifts towards isolating and purifying the target product, apalutamide API. This stage involves techniques similar to intermediate purification but tailored specifically for apalutamide.
- Extraction: The reaction mixture may be subjected to solvent extraction techniques to separate apalutamide from other components. The choice of solvent depends on the solubility profile of apalutamide and the impurities.
- Crystallization: Crystallization is often employed as a final purification step for apalutamide API to achieve high-purity crystals.
- Drying: The purified apalutamide crystals are carefully dried to remove any residual solvents and ensure proper storage stability.
Optimizing Production Efficiency and Quality
Throughout these production stages, a relentless focus is placed on optimizing two key aspects:
- Production Efficiency: Factors like reaction times, efficient mixing, and minimizing solvent usage are crucial for cost-effective production. Implementing automation and process control systems can further enhance efficiency.
- Product Quality: Stringent quality control measures are implemented at each step. Samples are analyzed to ensure the isolated intermediates and final product meet pre-defined purity specifications. This ensures the consistency and efficacy of the final apalutamide API.
The quality of Apalutamide API is contingent upon several factors:
- Adherence to GMP: Strict compliance with GMP regulations during the manufacturing process safeguards the quality and consistency of the final product.
- Rigorous Quality Control Procedures: Implementing robust quality control procedures at every stage of production is essential for identifying and eliminating potential impurities.
- High-Quality Raw Materials: Utilizing high-grade raw materials minimizes the risk of contamination and ensures the overall quality of the Apalutamide API.
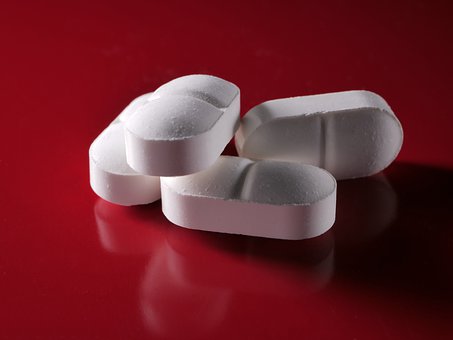
Synthesis of Apalutamide API
Apalutamide API possesses a well-defined molecular structure, characterized by the arrangement of its constituent atoms. This structure dictates its unique properties and therapeutic effects.
The synthesis of Apalutamide API involves a multi-step chemical process, often employing a series of well-established reactions. Here’s a closer look at the synthesis route:
- Reacting 2-hydroxy-3-trifluoromethylpyridine with sodium nitrite, sulfuric acid, sulfur dioxide, and other substances to obtain the diazotization product.
- Reducing the diazotization product using iron powder-acetic acid system to yield 2-cyano-3-trifluoromethyl-5-aminopyridine.
- Reacting with N-methyl-2-fluoro-4-bromobenzamide under appropriate solvent and conditions to obtain 1-[[3-fluoro-4-(methylaminomethyl)phenyl]amino]cyclobutane-1-carboxylic acid.
- Reacting with methanol to obtain the methyl ester compound 1-[[3-fluoro-4-(methylaminomethyl)phenyl]amino]cyclobutane-1-carboxylic acid methyl ester.
- Reacting with 2-cyano-3-trifluoromethyl-5-isothiocyanatopyridine under appropriate solvent and conditions to obtain apalutamide.
The entire synthesis process requires meticulous control of reaction conditions to ensure the purity and yield of the product. Different synthetic routes may vary in terms of yield, purity, and operational convenience.
Several factors can influence the efficiency and yield of Apalutamide API synthesis:
- Catalyst Selection: Selecting appropriate catalysts can significantly enhance reaction rates and selectivity, leading to higher yields of the desired product.
- Solvent Choice: The choice of solvent plays a crucial role in reaction efficiency. Selecting a suitable solvent can improve the solubility of reactants and intermediates, facilitating reaction progress.
- Reaction Temperature and Pressure: Maintaining optimal reaction temperature and pressure is essential for maximizing the desired reaction pathway while minimizing undesired side reactions.

Key Technologies and Challenges in Apalutamide API Synthesis
While advancements have been made in Apalutamide API synthesis, there are ongoing efforts to further refine the process:
1. Advancements in Apalutamide API Synthesis Methods
- Development of Efficient Catalytic Systems: Researchers are constantly exploring novel and efficient catalytic systems to accelerate reaction rates and improve the overall efficiency of the synthesis process.
- Implementation of Green Chemistry Principles: Integrating green chemistry principles into the synthesis is becoming increasingly important. This involves utilizing environmentally friendly solvents, minimizing waste generation, and employing energy-efficient processes.
- Application of Continuous Flow Synthesis Techniques: Continuous flow synthesis techniques offer potential benefits such as improved reaction control, enhanced product consistency, and reduced solvent usage.
2. Addressing Challenges in Apalutamide API Synthesis
- Optimizing Reaction Conditions for Selectivity and Yield: Continuously optimizing reaction conditions, including temperature, pressure, catalyst type, and solvent selection, remains a challenge to achieve the highest possible yield and purity of Apalutamide API while minimizing the formation of byproducts.
- Enhancing the Stability of Intermediates: Some intermediates involved in the synthesis can be unstable, potentially leading to yield losses. Developing methods to enhance the stability of these intermediates is crucial for improving the overall efficiency of the process.
- Developing Efficient Product Extraction and Purification Methods: Efficient methods for extracting and purifying Apalutamide API from the reaction mixture are necessary to obtain a product that meets the stringent purity requirements for pharmaceutical applications.
3. Quality Control Strategies for Apalutamide API Synthesis
- Monitoring Impurity Levels Throughout the Synthesis Process: Implementing robust monitoring procedures throughout the synthesis allows for the early detection and elimination of potential impurities.
- Implementing Rigorous Analytical Techniques: Utilizing a range of sophisticated analytical techniques, such as chromatography and spectroscopy, is essential for characterizing the Apalutamide API and ensuring it meets all quality specifications.
- Ensuring Adherence to Regulatory Standards: Strict adherence to relevant regulatory standards and guidelines governing the production of pharmaceutical ingredients is paramount to ensure patient safety and drug efficacy.
Conclusion
Apalutamide API plays a vital role in treating prostate cancer and holds promise for other androgen-sensitive malignancies. Its production involves a multi-step synthesis process adhering to stringent quality control measures. While advancements have been made in optimizing the synthesis, challenges remain in maximizing yield, minimizing impurities, and ensuring efficient extraction and purification. Continued research efforts are directed towards developing even more efficient, cost-effective, and environmentally friendly methods for Apalutamide API synthesis, ultimately paving the way for improved patient access to this life-saving medication.